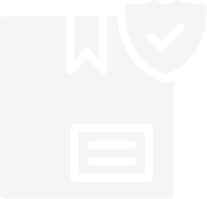
Industry 4.0
In smart factories, automated guided vehicles (AGVs) are used as transportation devices that carry sensitive cargo across production sites, or as connectors of the stationary machinery. These devices can navigate themselves and perform point-to-point deliveries, thanks to on-vehicle sensors that allow them to perceive and reason about their environment. The timeliness of the deliveries is crucial for the smooth operation of the factories, while safety is critical to avoid unwanted situations (e.g. collisions) that may cause delays, but also, severe damage to expensive equipment, or human workers. However, stalling transportation times and unwanted incidents may be observed in practice, due to a multitude of reasons, involving hardware failures within the device itself, on-vehicle sensor malfunctions, or unexpected encounters of obstacles, such as other AGVs, unattended objects, or pedestrians.
In this use-case, the EVENFLOW tools will be used to tackle challenges related to transporting goods in a smart factory. The EVENFLOW tools are used to learn how to identify and forecast incidents ahead of time, allowing the robot to timely adapt its behavior and modify its route. Importantly, such situations may be rare and manifest themselves in various ways that involve several risk factors. A special task in this domain is to endow the robot with self-inspection capabilities, allowing it to detect internal errors early-on and ensuring reliable operation. Additional desiderata include high update frequencies and low processing latency, which are a special challenge for the EVENFLOW tools, since mobile robots have limited computation power onboard as power consumption and weight matters so efficient communication and computation is necessary.